Southern Wine & Spirits
Warehouse Expansion
Lakeland, Florida
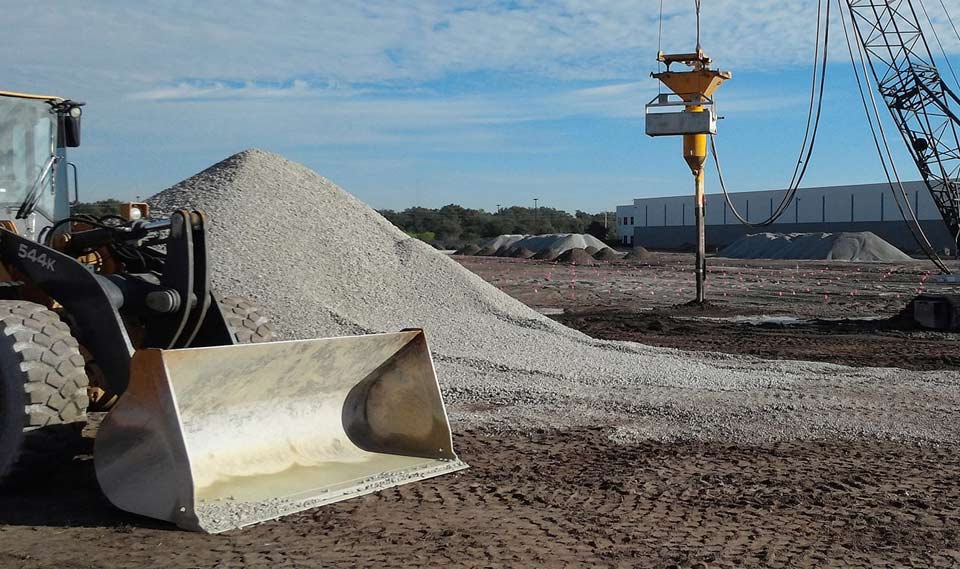
Client
Southern Wine & Spirits
Miami, Florida
Location
Lakeland, Florida
Related Services
Southern Wine & Spirits
Warehouse Expansion
We completed a geotechnical site investigation and construction monitoring/materials testing & inspection, including threshold inspection, for a proposed 440,000 sf expansion to an existing warehouse facility in Lakeland, Florida. The significant loading from the storage of a very high state-of-the-art rack system and associated tight settlement tolerance resulted in a need for soil improvement including both surcharging and vibro-replacement stone columns.
The connection of a new, heavily-loaded, warehouse directly connected with the same finish floor elevation as an existing warehouse that had been in use for years added challenges and utilized underpinning to prevent damage to the existing facility and differential settlement between the buildings. High water table along with poorly draining subgrade soils and heavy truck loading required extensive underdrains and a very robust free-draining rigid pavement section.
Geosynthetics were used for the poorer subgrade conditions. Challenges during construction associated with earthwork, foundation, and pavement subgrade preparation activities, along with high volumes of concrete cylinders and beams, plus the added duties of the anchor bolt and roof connection pull-out testing made this a unique and challenging project for us.
The expansion included:
- New parking areas
- Design and construction to rehabilitate of an existing rigid pavement system in great need of repair.
The construction included:
- 50-foot high tilt-up poured concrete walls
- Super-flat mat floor slabs
Field investigation included:
- Test pits
- GPR (Ground Penetrating Radar )
- ERI (Electrical Resistivity Imaging)
- SPT (Standard Penetration Test) Borings
- Muck probing to characterize the subsurface site conditions.
Madrid CPWG Approach
With the very high floor loading with high-density racking systems, along with fill and other loads, a maximum uniform load of 1,500 psf along with column, wall, and other loads, was evaluated for settlement which we estimated to be over 5 inches in some areas without soil improvement. Madrid CPWG provided recommendations for multiple soil improvement options including surcharge and aggregate piers. Aggregate piers were selected as the soil improvement method to speed up the construction schedule. A thorough investigation in areas of concrete (rigid) pavement that was cracking, with pumping water through cracks when trucks passed over, revealed silty sand installed directly under the pavement with a shallow water table. Underpinning was recommended to protect the original warehouse from settlement with the added loads from the addition. Madrid CPWG recommended a more robust pavement section consisting of GAB (graded aggregate base), an underdrain system, geotextile reinforcement, and a rigorous jointing pattern. Inspections continued throughout both day and night shifts to maintain the construction schedule.
Madrid CPWG Benefit
The heavily-loaded warehouse addition was attached to the existing warehouse without noticeable damage or settlement to the existing structure. The tight construction schedule was maintained throughout and the soil improvement methods utilized saved the owner money versus deep foundations and saved time versus surcharging the entire site. Trucks are now able to use the entire pavement drive areas without excessive bumps from broken concrete and the pavement section should last much longer than the original section did.